4 Manufacturing Trends that Are Impacting Metal Fabrication Today
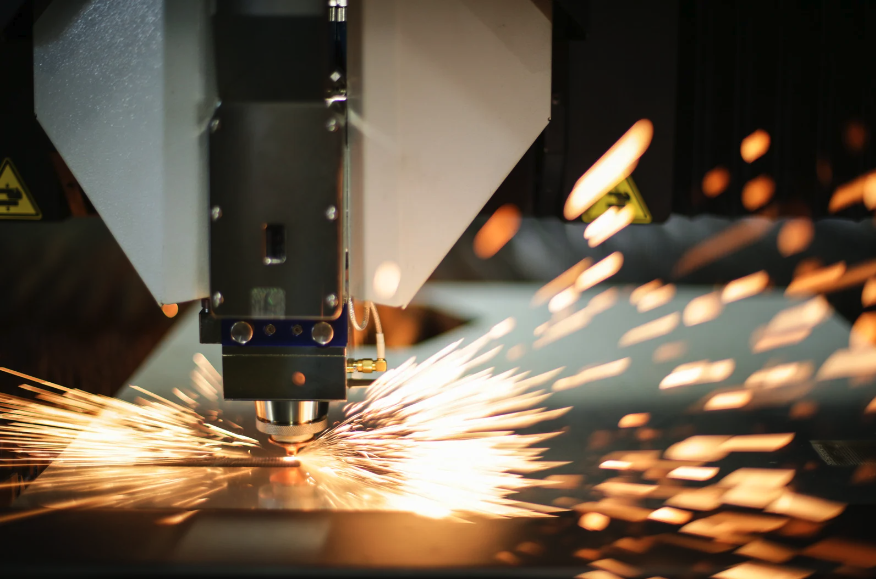
What does the future hold for metal fabrication?
A question like this can seem removed from the everyday challenges of manufacturers and their customers. But at ReNEW Manufacturing Solutions, we believe in staying ahead of industry developments because falling behind would compromise customer results. Manufacturing is evolving every day, and we’re committed to keeping pace. By monitoring trends and investing in the latest cutting-edge technology, we can offer the most competitive pricing, faster delivery times and unmatched quality for our customers.
Let’s explore the four key trends that are shaping the future of metal fabrication and driving our strategy at ReNEW.
1. The Growth of Laser Technology and the Importance of Strategic Adoption
Laser technology is improving rapidly, with power output increasing seemingly every day. It’s thrilling to watch the progress, and we already offer laser cutting as part of our metal fabrication services, allowing us to cut intricate details into a range of materials with fast turnaround times. Fiber lasers now excel at high-speed cutting and processing thicker materials, and traditional CO2 lasers are gradually being phased out in many applications.
However, we take a balanced approach to our investments. We're certainly impressed when we evaluate the latest lasers—but we carefully consider the trade-offs between power and speed, and compare these options to our traditional plasma machine. Any significant purchase must translate into better results for our customers, and we only adopt cutting-edge technology when we know it offers sustainable, lasting advantages.
2. Unlocking Efficiency With New Manufacturing Software
The concepts behind “Industry 4.0” have significantly impacted manufacturing over the last decade, and software integration has become crucial for greater efficiency. Our view is that software is now essential to remain competitive and deliver superior results, and we are proactive in searching for new solutions for our network of shops.
Our software portfolio currently includes fast quoting tools and diverse ERPs. We constantly evaluate machine monitoring software that can monitor capacity and maximize efficiency, as well as CAM software to streamline machine programming. Leveraging solutions like these allow us to take customers from initial quoting to final delivery as rapidly as possible.
3. Automation Can’t Fully Solve the Workforce Shortage
Manufacturing faces a labor crisis that is expected to intensify in the coming years. Some of the most skilled workers in many manufacturing shops are nearing retirement age, and the industry is struggling to attract enough young talent. While automation and robotics offer a partial solution, they are insufficient to fully resolve the labor crisis in metal manufacturing and other sectors.
At our facilities, we have increased our usage of automation to address this issue, employing cobots and part loaders. Delivery speeds have improved, and we’ll continue to invest in these technologies going forward. Yet we still find that these tools cannot replicate all the human skills that are essential to manufacturing success. We know manufacturing will remain a promising career path for young people who enjoy hands-on tasks.
To encourage young people to enter manufacturing, we offer on-the-job training programs. We seek out dedicated individuals and provide them with opportunities to become skilled welders or machinists. If an individual has the right attitude, we will put them in a place to succeed, regardless of their prior experience. A skilled workforce is critical to providing parts of the highest quality.
4. The Ongoing Growth of 3D Printing
3D printing has emerged as a mainstream fabrication method over the past decade, leading many in the industry to offer bold forecasts for its future. Some analysts suggested that 3D printing could soon revolutionize manufacturing, surpassing traditional machining in the process.
3D printing is an ideal choice for certain use cases, but we do not anticipate these bold predictions coming true in the near future. This manufacturing technology excels with polymers and has made strides in metal fabrication. However, metal 3D printing remains slow, making it ideal primarily for parts with very complex geometries. For most production volumes beyond prototyping, the time constraints are still too significant, and traditional machining remains the standard metal fabrication method.
At ReNEW, we recognize the strengths and limitations of both 3D printing and traditional machining, and we offer both services to our customers for their projects. We’re always ready to consult with our customers to determine the best manufacturing method for their parts to ensure quality and cost-effectiveness. In general, we still view 3D printing as a few years away from being able to handle medium- to high-volume production.
Embracing Technology for the Best Possible Results
At ReNEW, we take a progressive approach to manufacturing technology because we aim to surpass our customers’ expectations. We focus on the cutting edge to ensure we deliver the best quality with the fastest turnaround times and the most competitive pricing possible.
Request a quote today to see why our tech-focused approach sets us apart as a metal manufacturer.