CNC vs 3D Printing: How Should I Have My Part Made?
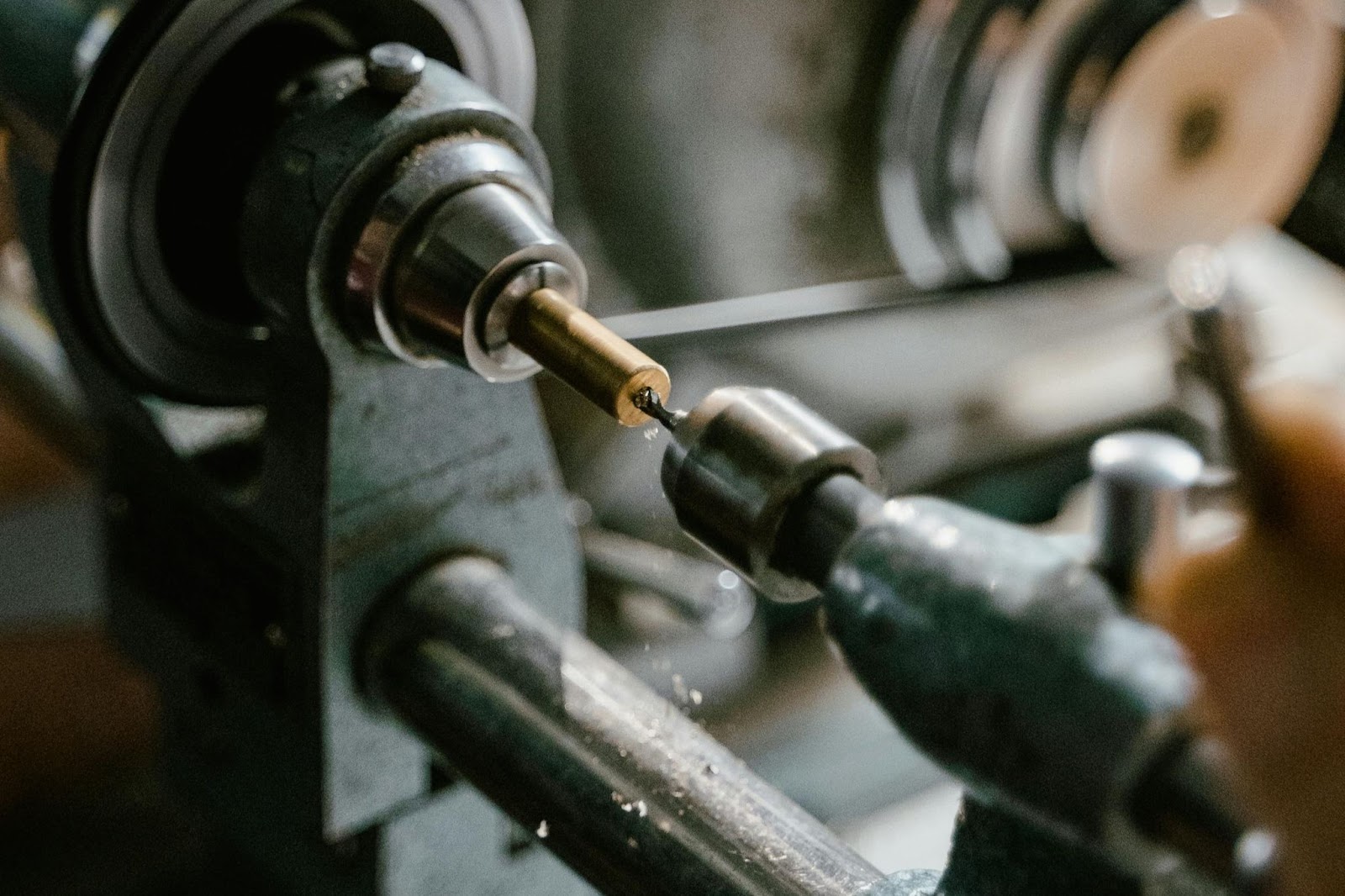
Advancements in manufacturing processes have many engineers considering their options when creating new parts during R&D or placing an order for a production run.
3D printing is now at a point where materials can be strong enough, and details can be fine enough to warrant the attention of manufacturers. However, CNC has long been a standby for producing parts in varying materials. Let’s walk through some of the core areas of comparison in CNC vs 3D printing techniques to help you decide which process is the right fit for your parts.
How to Choose: CNC Machining vs. 3D Printing in Parts Production
CNC Machining |
3D Printing |
|
|
Tolerances & Precision
CNC machining is the gold standard when it comes to precision and tight tolerances in parts production, beating out injection molding, 3D printing, and other common manufacturing techniques. If your parts need to respect micron-level tolerances, you may want to use CNC.
Surface Finish
Today’s 3D printers are not capable of producing polished end-state parts with fine, smooth surface finishes. If all you need are parts for fit and function, printing can be cost-effective and turn-time efficient. If you need exceptional smoothness, industrial CNC machines will produce superior results.
Feature Resolution
Both technologies are capable of suitably resolving feature details at sizes larger than a few millimeters. As feature sizes reach sub-millimeter levels, CNC gets an edge in resolution. However, both types of equipment can only resolve features as small as the tools (or nozzles, in the printer’s case) they’re equipped with.
Design Flexibility
Although both processes enjoy a lot of design flexibility, 3D printing gets an edge here since changes to the design are purely digital to the printer. With CNC machinery, changes may require you to account for time to retool and reprogram the machine (depending on what or how much has changed).
Part Complexity
Complexity is the primary cost throttle on CNC machined parts. There’s a cost for complexity since more complex parts require more time to machine, and more time = more money. This means that simple shapes are far faster and more efficient to produce with a subtractive CNC process than an additive 3D printing one, whereas more complex designs can sometimes be faster to produce on a printer.
With that said, CNC machining equipment is capable of extreme levels of precision on intricate parts that outstrips 3D printing, which means a choice to use CNC can make sense when:
- You need only small quantities (like prototypes) or;
- whenever the part would be impossible to manufacture with another process.
Part Size
Size is the primary cost throttle on 3D printed parts. Larger parts take more materials and more time to build up from nothing in an additive process, which will tend to favor a subtractive CNC machining process that starts with a large stock and removes material to reach the desired shape.
Cycle Times & Part Quantities
The two technologies diverge in cycle times and production scalability depending on the size and complexity of the parts. With very small parts that have high geometric complexity, 3D printing can be extremely cost and time-efficient compared to CNC. However, CNC cycle times will be much quicker as the size of the part increases and/or the complexity decreases.
A printing process is generally used in prototyping and small batch production, but not for high volume runs. At the highest quantities (tens of thousands or even millions), injection molding becomes an alternative with faster cycle times than 3D printing. However, it takes a very large number of parts to justify the setup costs of tooling and mold creation.
CNC can be used at any part volume, but excels in small volumes on complex parts and large volumes on simple ones.
Material Options
Commonly associated with plastic polymers, modern industrial 3D printers can actually utilize a wide range of materials. Printers can create parts from plastics, powders, resins, metals, and even carbon fiber. This broad selection makes the technology very promising as it grows into new applications, from aerospace and machinery components to customized consumer products.
In addition to the many familiar plastic polymer options, 3D printing resins could include flexible or elastic options like rubber or silicon and 3D printing metal powders are made from titanium, stainless steel, aluminum, tool steels, nickel alloys, and many other metals.
CNC machining has even more material versatility. If it can be cut, grinded, or milled, it can be machined into a finished part using CNC equipment. CNC machines often work with metals but also handle wood, plastics, composites, and other materials.
Structural Strength
Additive 3D printing processes tend to use polymers and composites, some of which are fairly strong, but most are still better relegated to applications with non-structural loads. CNC machined parts will exhibit whatever strength is inherent in the material you’ve machined.
Temperature Limits
The materials used in modern industrial 3D printing can often survive high temperature environments for extreme applications. However, CNC machined metals will typically outmatch printed parts by a wide margin in their temperature tolerances — which will be based on the metals used.
CNC Machine vs 3D Printer: What’s the Verdict?
CNC manufacturing still has numerous advantages over 3D printing for parts that demand extreme precision, tight tolerances, the strongest materials, and the finest features and finishes. However, for parts that are relatively small and would require extensive tooling time due to geometric complexity, 3D printing can be a quicker and more cost-efficient option. Printed parts are also still popular for prototyping, where the raw design flexibility of additive manufacturing really shines.
Whichever process you need, it’s imperative that you work with an experienced provider of 3D printing or CNC machining services. Contact ReNEW Manufacturing Solutions today to share the details of your project, and we’ll offer guidance on the best approach.