Welding Cobots & the Future of Robots in Manufacturing
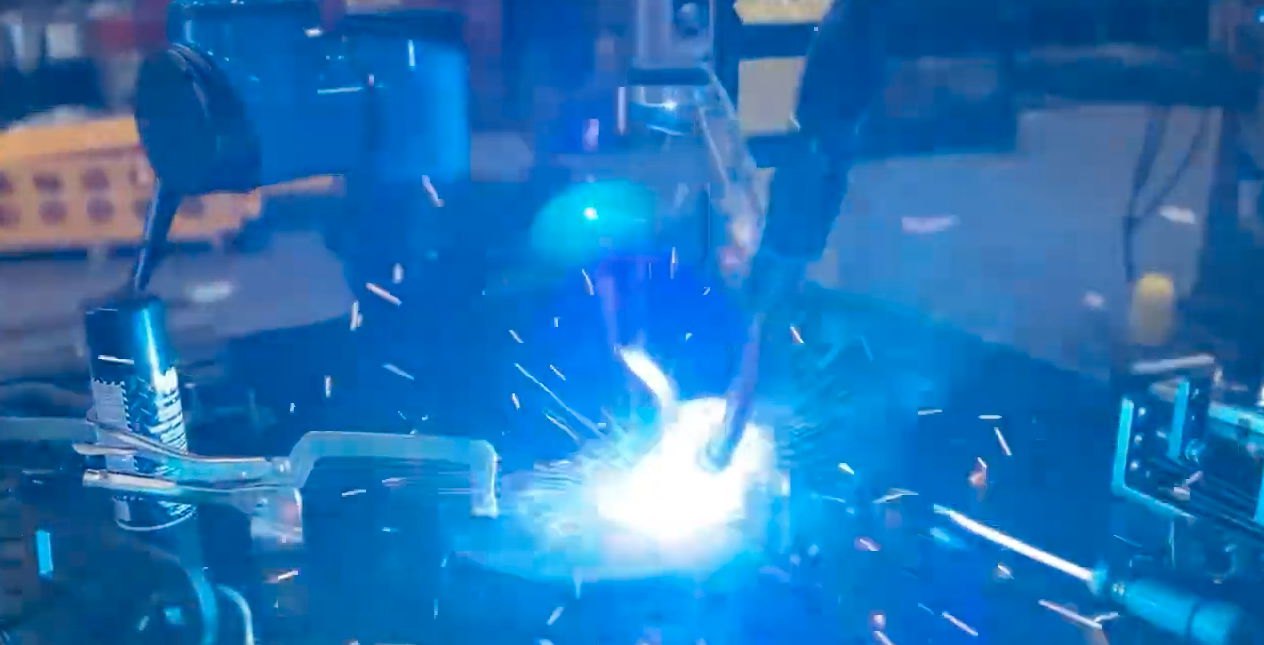
Robots and “cobots” (collaborative robots) are some of the biggest trends impacting manufacturing these days. While most of the large-scale production operators are already deploying robotics, the International Federation of Robotics (IFR) predicts that more than half of all manufacturers will be working with robots within the decade — regardless of size.
With continued labor shortages and another wave of workers hitting retirement age soon, manufacturers have increasingly turned to robots in manufacturing to streamline operations and accelerate production.
Research shows that manufacturers are investing heavily in automation. Industrial robots in manufacturing grew by 12% in 2023 with new investments in the automotive, electronics, electrical, and fabrication industries. Today, there are some 3.4 million manufacturing robots in place globally.
Types of Cobots in Manufacturing
The are four main types of cobots being deployed in manufacturing:
- Power and force limiting cobots: These are tailored to detect human interaction and stop activity. These are generally used in compact applications and eliminate the need for safety enclosures.
- Safety-rated + monitored stop cobots: This type of cobot can detect when someone enters a designated area and pause operations until they leave. This reduces the need to restart manually.
- Fenceless cobots: Also called speed and separation, these cobots slow down when movement is detected and stop completely if someone gets too close.
- Hand-guided cobots: Hand-guided cobots enable workers to guide the robot to new positions or move between stations.
Welding Cobots
One such use is a collaborative welding robot. Cobot welding automates the welding process, reducing the time it takes to join metals, and improving accuracy and safety. For example, the TIW Machine and Fab team uses collaborative welding robots to deliver improved arc performance, strengthen weld quality, and significantly improve throughput. Cobots in manufacturing can load and unload from a single station, which can be shared with the robot envelope. This is ideal for high-mix, low-volume operating scenarios.
Collaborative robot welding can be used for various types of welding including:
- Arc welding
- Resistance welding
- Spot welding
- Tungsten inert gas (TIG) welding
- Metal inert gas (MIG) welding
- Laser welding
- Plasma welding
Using a welding cobot still requires human interaction to program devices, move the arm, and change parameters for jobs. The welding itself takes place automatically, providing a consistent and durable weld.
Benefits of Using a Cobot Welder
For manufacturers and suppliers, a welding cobot produces significant benefits, including:
- Increased efficiency: Robotic welders can operate 24/7, delivering faster completion times and higher output compared to human workers who require breaks and time off.
- Enhanced safety: Equipped with advanced safety features, robotic welders protect workers from welding arc hazards, high temperatures, and bright lights, creating a safer work environment that boosts productivity and job satisfaction while reducing injury risks and associated costs.
- Improved accuracy: Excelling at repetitive tasks, robotic welders maintain consistent attentiveness and precision throughout large-volume projects, minimizing errors that manual welders may eventually make due to human limitations.
- Reduced waste: With their superior accuracy, robotic welders generate less waste from mistakes, ensuring efficient material usage and minimizing the need to discard improperly welded or weakly joined parts.
- Lower delivery costs: Despite higher initial costs, the high productivity of robotic welders ultimately offsets the investment, enabling welding companies to accomplish the same workload with fewer operators, trim overhead expenses, and offer competitive pricing or additional services to clients.
Cobotics is also helping to bring manufacturing back from overseas. There has been a significant increase in onshoring activity since the massive supply chain disruptions a few years ago that left many OEMs idle waiting for components to be shipped from overseas. By reducing labor costs and accelerating production, manufacturers can compete more cost-effectively. CNC and robotics in manufacturing make this shift possible.
Get High-Quality Machined and Fabricated Parts
ReNEW Manufacturing Solutions companies produce high-quality machined and fabricated parts to exact tolerances. Using the latest advances in manufacturing robotics and cobots. With three facilities, 227,000 square feet of production space, and a fleet of 50+ machines, ReNEW Manufacturing Solutions offers precision manufacturing expertise for welding and fabrication, CNC machining, finishing, sub-assemblies, parts manufacturing, laser cutting, forming, and contract manufacturing.
Connect with the machining experts at ReNEW Manufacturing Solutions to discuss your business opportunities and your future.