What's The Difference Between Welding and Fabricating?
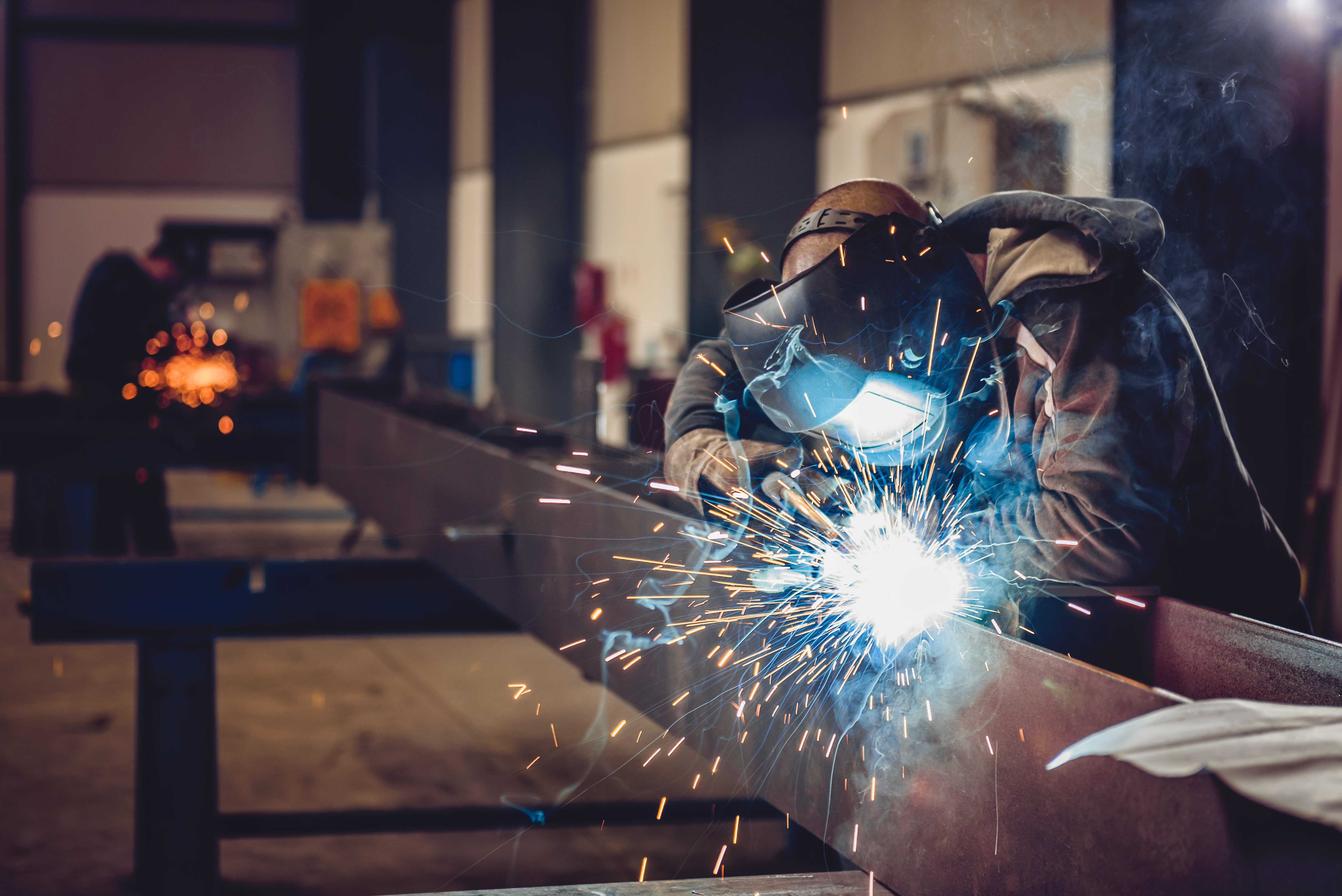
While welding and fabricating are overlapping terms that may, at times, be used to refer to the same process, there are actually distinct differences.
- Fabrication is a more inclusive term that refers to the overall process of metal manufacturing. It may or may not include metal welding. Put simply, fabrication is making a product out of metal.
- Welding involves joining together two pieces of metal — forming a permanent bond — with an application of heat to the contact area between the parts. Welding is one type of metal fabrication process.
A welder and fabricator often work together to complete work as many projects require both. In some cases, one person may have experience as both a welder and fabricator.
Let’s take a closer look at the processes involved in welding and metal fabrication to get a better idea of what’s involved.
Metal Fabrication Techniques & Machinery
Each fabrication service provider may offer different capabilities, but here are some of the most common options along with the tools used:
- Cutting: Shears, saws, lasers, or plasma cutters
- Bending: Press brakes or roll benders
- Punching: Punches or dies
- Drilling: Drill presses or CNC machines
- Shearing: Shears or guillotine shears
- Forming: Roll forming, stretch forming, or hydroforming machinery
- Stamping: Mechanical or hydraulic presses
- Machining: Lathes, mills, or CNC machines
- Grinding: Surface grinders or belt grinders
- Finishing: Painting, powder coating, or plating
Key Benefits of Metal Fabrication
Below are the core benefits of utilizing metal fabrication in parts manufacturing:
Customization |
Allows for the creation of custom-designed products tailored to specific requirements or applications. |
Precision Engineering |
Enables the production of intricate components with high precision and accuracy, ensuring quality and reliability. |
Innovation |
Facilitates the development of new technologies and products by pushing the boundaries of material capabilities and manufacturing processes. |
Material Versatility |
Can work with a wide range of metals to suit various project needs. |
Cost-Effectiveness |
Cost-effective for both small and large production runs depending on the complexity of the design. |
Strength and Durability |
Offers exceptional strength and durability for long-lasting applications. |
Design Flexibility |
Can produce complex shapes and designs that might be difficult or impossible with other methods. |
Sustainability |
Adaptable to incorporate recycled metals, reducing environmental impact. |
Metal Welding Techniques
Metal welding processes can take different forms depending on the needs of metal fabricators and welding requirements. The most common are variations of solid-state welding or fusion welding. Fusion welding heats metal pieces and then adds a filler to join them together. Solid-start welding does the same but without needed additional additives.
These two types of metal welding may use different techniques and tools, such as:
- Metal Inert Gas (MIG)
- Tungsten Inert Gas (TIG)
- Brazing
- Gas Metal Arc Welding (GMAW)
- Shielded Metal Arc Welding (SMAW)
- Flux-Cored Arc Welding (FCAW)
- Plasma Arc Welding
- Gas Tungsten Arc Welding (GTAW)
- Submerged Arc Welding (SAW)
- Laser Beam Welding (LBW)
Welding may be done by hand or robotics. Robotic welding automates the process to save time and produce better results. There is also less material waste. Humans still supervise the process and you get consistent and high-quality results each time from robotic welding.
Key Benefits of Metal Welding
Permanent Joining |
Creates strong, permanent joints between metal components. |
Versatility |
Can be used to join various metals and thicknesses. |
Strength |
Joints can be as strong, or even stronger, than the base metal. |
Efficiency |
A fast and efficient method for joining metal components compared to other techniques like riveting. |
Sealing |
Certain techniques can create airtight or watertight seals. |
Heat Distribution |
Allows for controlled heat application, minimizing distortion in the surrounding metal. |
Automation Potential |
Can be automated for high-volume production and improved consistency. |
Repair Applications |
A valuable tool for repairing cracks, breaks, and other defects in metal components. |
From laser cutting to forming to machining and welding, ReNEW Manufacturing Solutions has cutting-edge tools and highly skilled operators to bring your designs to life. You get affordable, high-quality components that meet the most exacting specifications.
Need metal fabrication and welding from industry-leading experts? Contact ReNEW today to request a quote.