Where to Find Manufacturing Productivity Gains Amid the Labor Shortage
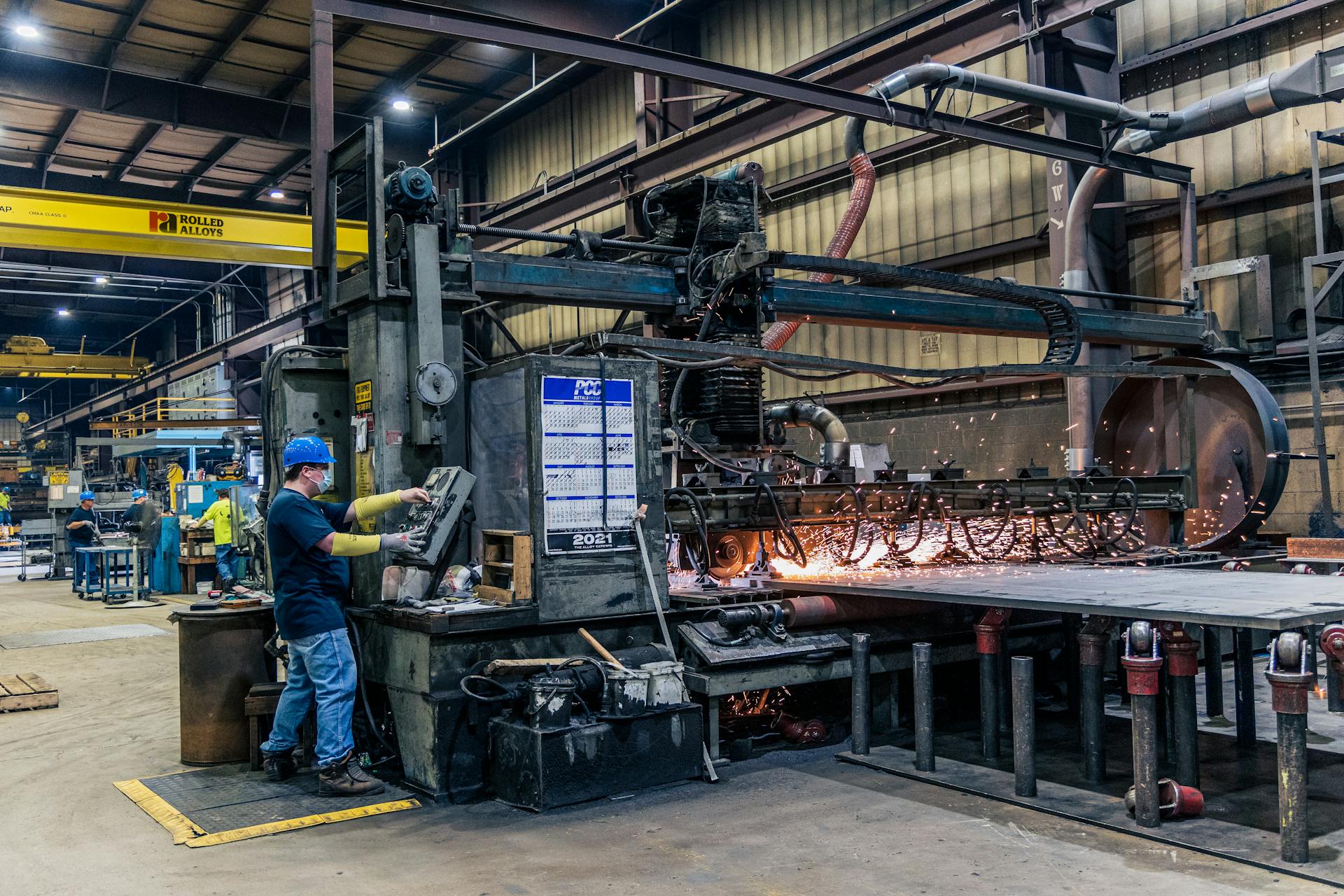
It’s been a challenging few years for anyone in the manufacturing industry. Supply chain disruption, inability to get raw materials and components, and sudden price hikes continue to cause stress. However, the growing labor shortage tops the list of problems facing American manufacturing.
The National Association of Manufacturers (NAM) says attracting and retaining a quality workforce is the top business challenge of its members. A Deloitte study says the industry will require 3.8 million jobs to be filled over the next decade. Yet, fewer younger people are entering the trade, more workers are hitting retirement age, and there’s a growing skills gap in between.
The North American manufacturing industry has made a remarkable comeback — adding some 800,000 new workers over the past two years — but more talent is needed. With labor shortage in manufacturing persistent, manufacturers need to find ways to drive productivity and likely do it with fewer employees.
Manufacturing Productivity
Overcoming the manufacturing labor shortage requires innovative solutions. Digital transformation is underway in earnest. Industry 4.0 solutions are unlocking significant value.
Companies that are embracing robotics and cobotics, advanced automation, additive manufacturing, and Internet of Things (IIoT) connectivity are seeing significant results. A McKinsey analysis shows that these innovations can:
- Improve labor productivity in manufacturing by 15-30%
- Eliminate 30-50% machine downtime
- Increase throughput by 10-30%
- Save 10-20% on cost-of-quality
- Reduce inventory holding costs by 15-20%
How to Increase Manufacturing Productivity
Combined with lean production strategies to reduce waste and provide continuous improvement, modern manufacturing is showing significant gains in productivity on the factory floor.
Automation Is Key
For example, lights-out machining with CNC technology removes the need for continuous attention from operators. The right 5-axis CNC machine, for example, can run unattended overnight or on weekends. Some machines can operate for up to 14 hours in unattended mode, creating consistent quality production.
Fixed automation handles a continuous workflow with set tasks. Programmable automation is often used for batch production, enabling changeovers based on batch sizes and lead times. Flexible automation, such as a CNC machine, includes precise controls for rapid changeover, allowing for increased customization and scalability. Integrating devices and machines together using a central control plane allows for tight control and more efficient sequencing of events. Sensors provide real-time monitoring for granular control and quality assurance.
Leveraging Data
Real-time data is also driving productivity. Today’s smart machines can predict the likelihood of failure and when it is most likely to happen. Repairs can be done at optimal times, reducing overall downtime with preventative maintenance.
By monitoring high-value KPIs, manufacturers are also tracking productivity in a much more robust way, focusing on KPIs such as:
- Overall Equipment Effectiveness (OEE)
- Production yield
- Downtime and cycle times
- Rework
- Cost per unit
This data helps uncover areas to improve and optimize production scheduling and forecasting.
Increase Productivity in Manufacturing
Automation, robotics, and data platforms all have the potential to improve manufacturing productivity, worker safety, and overall results. When you contract with a manufacturing company that deploys the latest technology solutions, you can be confident you will be getting components that meet your exacting quality requirements.
For instance, ReNEW Manufacturing Solutions saw an opportunity to improve our quoting process by implementing Paperless Parts, eliminating manual data entry, duplicative work, and human error from the front office through to the shop floor. The result has been that our location general managers now have the streamlined process and efficiency to get to quotes quickly, satisfying customer demands for fast quote turnaround times and winning more business.
We’ve also made strategic investments in automated robotic welding machinery — with a Copilot Collaborative Welding System from Miller — for rapid and reliable throughput. This advanced automation solution accelerates and standardizes high-quality results across various welding processes, including Gas Metal Arc (GMAW), advanced arc pulse (GMAW-P), and Regulated Metal Deposition (RMD). See it in action on our LinkedIn!
ReNEW Manufacturing Solutions has made it our mission to renew American manufacturing, bringing together fabrication and machine shops and helping modernize and scale resources to improve productivity and compete effectively with the latest CNC technology. These manufacturers often feel the greatest impact in a tough market and may not have the resources to invest in the latest technology. ReNEW Manufacturing Solutions works with business owners and investors to find opportunities — whether you are looking to find a new home for your business or attract additional investments to modernize.
The ReNew Manufacturing Solutions family of manufacturing companies also delivers superior quality manufacturing services at fair prices. Serving OEMs, Tier 1 suppliers, and others nationwide, we provide components, parts, and subassemblies faster than the competition, leveraging innovative technology that drives productivity in manufacturing, Get a quote today.
Connect with ReNEW Manufacturing Solution to discuss your business opportunities and your future.